
Keep in mind that we need to take care not to exceed the level deviation the operator gave to us. This will be our process gain variable, or Kp. Find the Dynamics of the ProcessĪt this time, we need to find out how much a change in gain affects our change in level. Additionally, be sure the lag is zero, and in the test menu, set the tank size to “large”. We’ll start with default settings, however, set the loss on your level simulator to zero. Set up the SimulatorĪt this time, we’ll be using the simulators that we built. In this case, we are using a simulator and not tied to a real world process. Keep in mind that if we run the tank empty, you might want to make sure your load has the ability to pull product from another source. One option is to kill the flow pump if the tank gets close to overfilling. Take care not to exceed these limits when tuning.Īlways have a safety in place in the event that we do overfill the tank. Before we begin, talk to the operator to see how much deviation we are allowed on the tank level. It’s important to realize that varying the tank level will also vary the head pressure to the load. Likewise, we don’t want the tank to run empty if we are running production. Obviously, we do not want to overfill the tank. Warning about Tuning a PID for Tank Level For surge tanks, which are fast moving processes you will need a different method. The tuning method we’ll use here is for slow moving processes. If you don’t have the ability to perform a step change, you can calculate the dynamics by determining the volume of the tank, and the flow rate of your pump. We might need to perform a step change to determine the dynamics of the process. In this example, we will take open loop control of the tank (manual) for tuning the PID. Since we already have the flow controller tuned, we will concentrate on the level PID controller. In this example, our level PID will provide a setpoint to the flow controller. Therefore, a given change in output will only change the temperature by a certain amount.Ĭonsider the following process of a linear tank: For example, we have ambient losses, electrical losses, and losses due to the load. With temperature control, the higher our temperature, the more losses we have. This is different than a self-regulating process such as temperature. Assembly Registers and Compatibility Modes.FactoryTalk View SE Trends and Data Log.Beginning a FactoryTalk View SE Project.Derivative Settings for ControlLogix PID Enhanced.
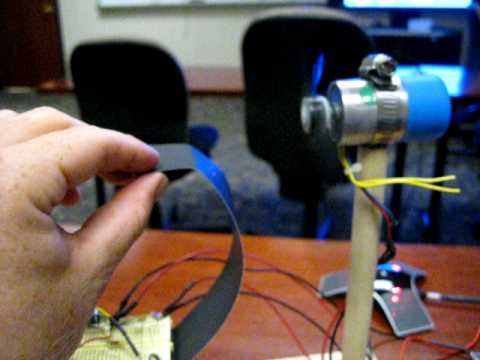
Integral Settings for ControlLogix PID Enhanced.Proportional Settings for ControlLogix PID Enhanced (PIDE).Proportional, Integral, Derivative (PID).
